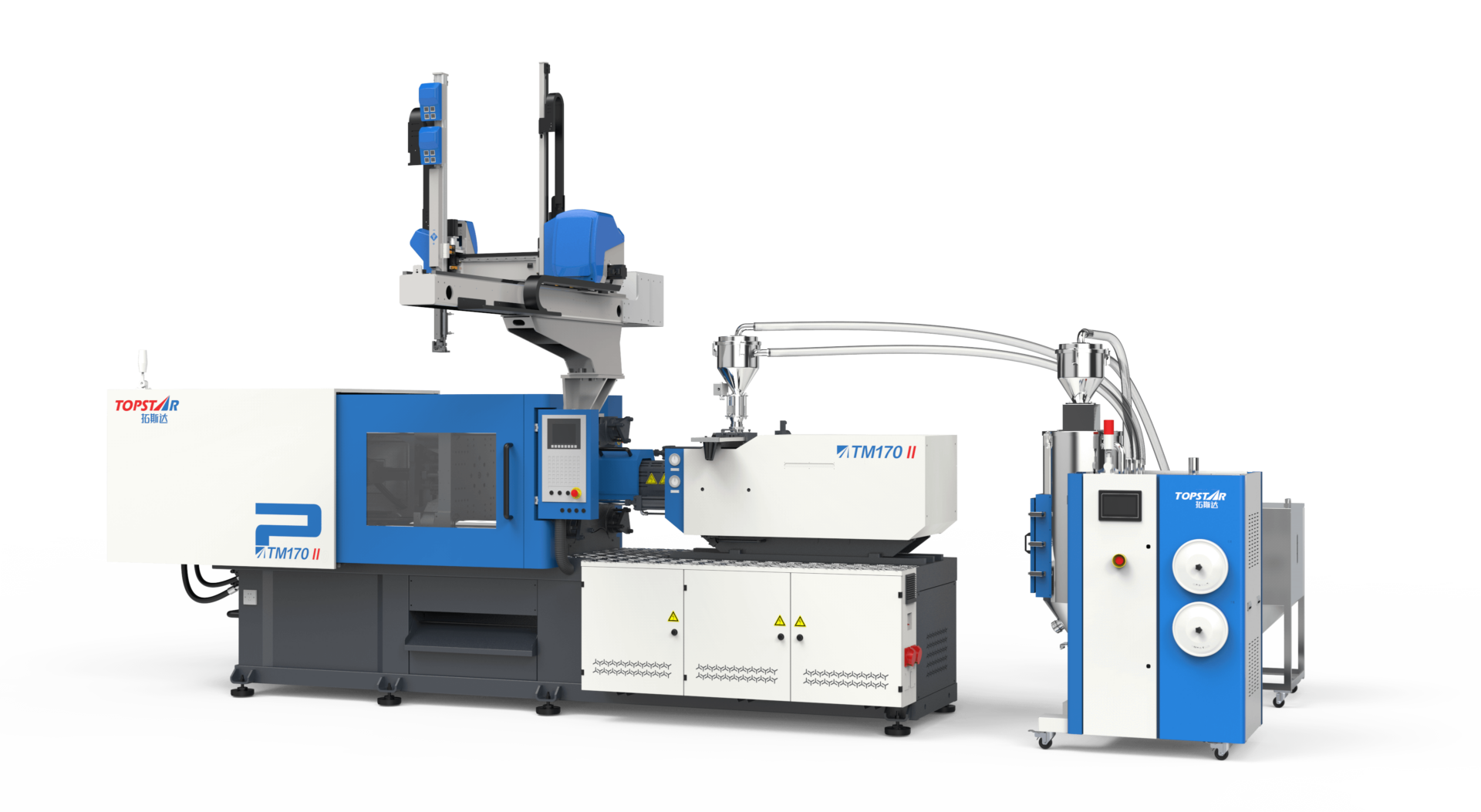
There are many different injection molding machine types to choose from. The best injection molding machine must be the one that best suits your company’s production needs and manufacturing. In this article, we will educate you on the types on the market, as well as what characteristics they have and what occasions they are suitable for.
Two different types of injection molding machines: vertical and horizontal injection molding machines
Vertical and horizontal injection molding machines are two pieces of equipment commonly used for injection molding in the plastics manufacturing industry. Horizontal injection molding machines adopt a horizontal layout, and the injection and clamping devices are arranged horizontally. Due to their ability to operate efficiently and accommodate multi-cavity moulds, they are often used to produce large, complex parts in high volumes. Horizontal injection molding machines are ideal for applications requiring precise injection parameter control. This level of control ensures consistent quality and precision, making it suitable for manufacturing components in automotive and medical applications.
Vertical injection molding machines use a vertical layout with the injection unit positioned vertically above the mould. They are suitable for small and medium-sized batch production of small and medium-sized parts and can save space. Vertical injection molding machines are typically used for over-moulding or insert molding applications, where auxiliary materials or components are encapsulated within the moulded part. The process is beneficial for adding features such as washers, threads, or metal inserts to plastic parts.
Hydraulic injection molding machine
Hydraulic injection molding machines are relatively traditional and standard equipment in the plastic manufacturing industry. These machines use hydraulic systems to create pressure, injecting molten plastic into moulds to produce finished parts. Their ability to generate high clamping forces enables the precise moulding of large, complex parts. At the same time, hydraulic injection molding machines are versatile and suitable for various materials, including thermoplastics, thermosets, and elastomers. In addition, they feature rugged construction and can withstand harsh operating conditions and heavy-duty production environments. The disadvantage is that it requires inspection and maintenance and is not friendly to the production environment.
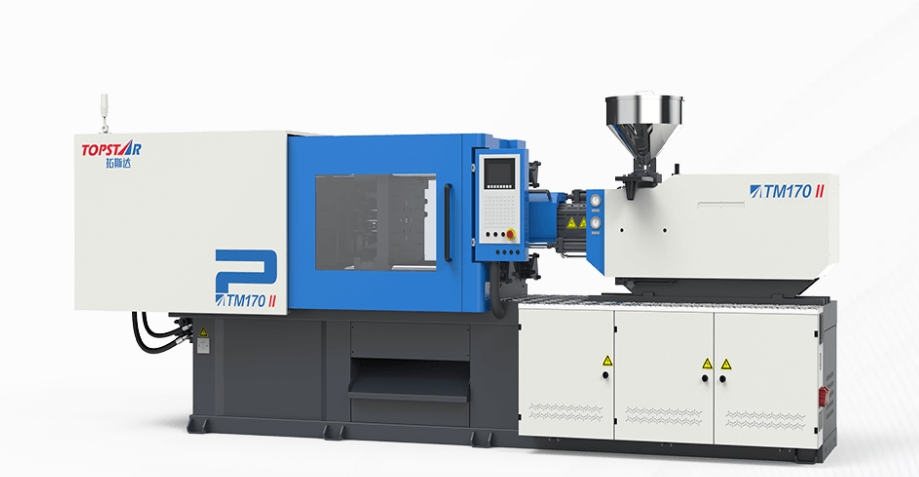
Electric injection molding machine
An electric injection molding machine is a relatively efficient modern manufacturing equipment. Electric servo motors operate all their machine movements. Compared to hydraulic machines, electric injection molding machines eliminate the need for hydraulic oil and reduce energy consumption during operation. Electric servo motors also precisely control machine movement, including injection speed, pressure, and position. During operation, they are quieter because they do not rely on hydraulic pumps and motors that create noise. Electric injection molding machines also do not require hydraulic oil, reducing the risk of oil leakage and contamination. They are ideally suited for use in the production of medical devices and components used in equipment, and their clean and quiet operation combined with precise control ensures compliance with strict regulatory standards for medical-grade materials and products.
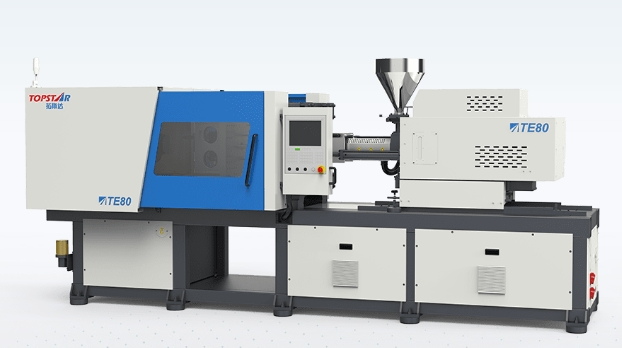
Hybrid injection molding machine
Hybrid injection molding machines combine the advantages of hydraulic and electric injection molding machines. Their injection devices use servo drive motors, and their mould clamping devices use hydraulic systems. Energy-saving operation is achieved with this configuration because the electric motor consumes less energy than a conventional hydraulic system, especially during low speeds and idling, and the electric injection unit allows precise control of injection speed, pressure, and position. Using hydraulic power as the clamping unit provides high clamping forces, and hybrid injection moulding machines are generally more environmentally friendly due to reduced energy consumption and lower carbon footprint. These machines’ hybrid nature allows manufacturers to balance performance and energy efficiency, making them popular for various injection moulding applications in the medical, packaging, consumer goods, and electronics industries.
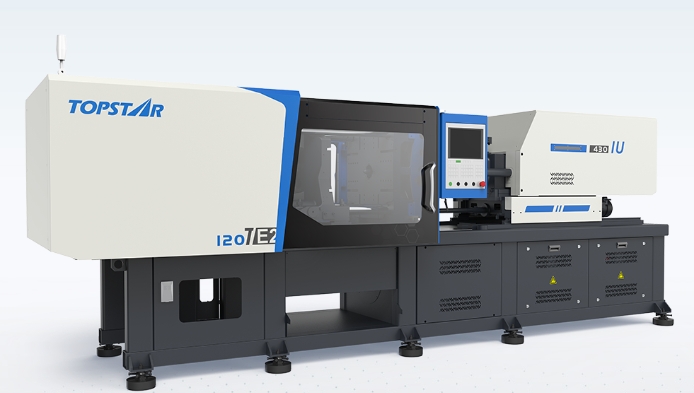
Choose the machine that works best for you.
When combining the injection molding machines mentioned in this article, you must also consider factors such as the product’s type, throughput, material properties, required accuracy, cycle time, and budget constraints. The first step is to determine the type of product you are making. Electric injection molding machines are suitable for the mass production of small and medium-sized parts. Conversely, choose a hydraulic injection molding machine with high tonnage capacity and a more oversized platen for large parts or low-volume production. Next, consider the material properties of the product. Thermoplastics, thermosets or elastomers, for example, may require a specific injection molding machine with precise temperature control, injection pressure and screw design to achieve optimal results. Another important consideration is energy efficiency, which can significantly reduce operating costs and environmental impact.
Find your perfect match!
The best injection molding machine is the one that meets your specific needs, requirements, and production goals. You can find the equipment that best suits your injection moulding needs by considering injection molding machine type, size, performance metrics, energy efficiency, and more.
TRENDING POSTS
- What factors can cause delays in the injection molding process of plastic molding machine? 2024/03/20
- Exhibition Review| Topstar participates in InterPlas Thailand 2024 2024/03/20
- Star Case | Topstar helps Santong upgrade its intelligent plant 2024/03/20
- Topstar Special | National Science and Technology Workers Day 2024/03/20
HOT TOPIC
- .ervo motor-driven linear robots
- 3 axis robot
- 3 axis robots
- 3 in 1 Compact Dehumidifying Dryer
- 3-axis robot
- 3-axis robots
- 5-axis CNC machine
- accuracy
- Air Chillers
- all electric injection molding machine
- all electric injection molding machines
- All-electric injection molding machines
- and overall production quality. Therefore
- AP-RubberPlas
- automated injection molding machine
- Automation changed engineering
- automation of injection molding robots
- auxiliary machine
- Bench Injection Molding Machine
- Cabinet dryer manufacturers
- Cabinet dryers
- chiller
- CNC Drilling Machine
- CNC Drilling Machines
- cnc engraving machine manufacturer
- cnc laser cutting machine manufacturer
- CNC machine
- CNC Machine Center
- CNC Machine for Sale
- CNC Machine Manufacturing
- CNC Machine Tool
- CNC machine tool product
- CNC Machining Center
- CNC wood carving machine
- Cooling system
- Cross-Walking Single Axis Servo Cylinder Robot
- Cross-Walking Single-Axis Servo Cylinder Robot
- Cross-Walking Three-Axis/Five-Axis Servo Driven Robot
- cross-walking three-axis/five-axis servo-driven robot
- Dehumidifier Dryer
- Dehumidifying Dryer
- delta parallel robot
- Desktop Injection Molding Machine
- Desktop injection molding machines
- Desktop Molding Machine
- desktop plastic injection machine
- Desktop Plastic Injection Molding Machine
- direct clamp injection molding machine
- Direct clamp injection molding machines
- Dosing & mixing system
- Drilling Centers
- Drying and dehumidification system
- drying and dehumidifying equipment
- Drying and Dehumidifying System
- drying system
- effective and efficient. Cabinet dryers are also used in other industries where large quantities of material need to be dried
- efficient injection molding machine
- elbow hydraulic injection molding machines
- electric injection molding machine
- electric injection molding machines
- energy-efficient injection molding robot
- energy-saving injection molding machine
- etc. Among injection molding robots
- exhibition
- features of CNC machine
- Feeding And Conveying System
- Five Axis Machine Center
- Fully automatic injection molding machine
- Gathering Topstar
- giant injection molding machine
- GMU-600 5-Axis Machining Center
- Granulating & Recycling System
- Heavy duty injection molding machine
- High-precision electric molding machines
- high-precision plastic molding machines
- high-speed all electric injection molding machine
- Honeycomb rotor dehumidifier
- horizontal injection molding machine
- Horizontal Injection Molding Machines
- Horizontal Injection Moulding Machine
- Horizontal Mixer manufacturer
- How The CNC Machine Works
- hybrid injection molding machine
- hydraulic injection molding machine
- Hydraulic Injection Molding Machines
- in this article
- Industrial robot
- Industrial Robot Chinese brand
- industrial robot parts
- industrial robot supplier
- Industrial robots
- Industry Chain
- Injection Manipulator
- injection manipulator robot
- injection mold machines
- Injection molding
- Injection molding automation
- Injection Molding Automation Solution
- injection molding dryer
- Injection molding equipment
- injection molding hopper dryer
- Injection molding machine
- injection molding machine brand
- Injection Molding Machine Factory
- Injection Molding Machine Manufacture
- Injection molding machine manufacturer
- injection molding machine manufacturers
- Injection molding machine procurement
- injection molding machine robotic arm
- injection molding machine with a robot
- Injection molding machines
- injection molding material dehumidifying
- injection molding plant
- Injection Molding Robot
- injection molding robot arm
- Injection molding robot automation
- Injection molding robotic arm
- injection molding robots
- Injection moulding machine
- Injection Moulding Robots
- Injection Robot
- Injection robot arm
- Injection robot manufacturer
- Injection robot wholesale
- injection robots
- intelligent injection molding machines
- Introducing Injection Robot
- It is the best choice for drying large quantities of material at once. Cabinetmakers use these machines because they are fast
- large injection molding machine
- Learn what industrial automation and robotics is
- linear robot
- linear robots
- low speed sound-proof granulator
- machine plastic molding
- make sure to add some! Improvements (2) Keyphrase in introduction: Your keyphrase or its synonyms appear in the first paragraph of the copy
- manipulator machine
- manufacturing
- medical grade injection molding machines
- medical injection molding machine
- medical injection molding machines
- micro injection molding machine
- middle speed granulator
- Mini CNC machine manufacturers.
- Mold Temperature Control System
- mold temperature controller
- mold temperature controllers
- molding material Dehumidifying System
- mould temperature control system
- mould temperature controller
- mould temperature controllers
- New electric injection molding machine
- nitrogen dryer manufacturer
- nitrogen dryer system manufacturer
- Oil type mold temperature controller
- Oil type mold temperature controllers
- open day
- Outbound links: No outbound links appear in this page. Add some! Images: No images appear on this page. Add some! Internal links: No internal links appear in this page
- PET Preform injection molding
- phone case maker machine
- phone case making machine
- plastic bottle making machine
- plastic bottle manufacturing
- plastic bucket making machine
- plastic bucket manufacturing
- Plastic chair making machine
- plastic forming equipment
- plastic hopper dryer
- plastic injection machine
- plastic injection machines
- plastic injection molding
- Plastic injection molding equipment
- Plastic injection molding machine
- Plastic Injection Molding Machines
- plastic injection moulding machine
- plastic injection robot
- Plastic Molding machine
- Plastic Molding Machines
- plastic molding press
- plastic moulding machine
- plastic phone case making machine
- plastic-molding machine
- powerful granulator
- Powerful Type Sound-Proof Granulator
- precision injection molding
- precision injection molding machines
- production of plastic seats
- pure water mould temperature controller
- Robot injection molding
- robot injection molding machine
- robot manufacturing companies
- Robotic arm for injection molding machine
- robotic injection molding machines
- robotics in injection molding
- SCARA robot
- SCARA robots
- Service-oriented manufacturing
- Servo Cylinder Robot
- servo driven robot
- Servo Driven Robots
- servo injection robots
- servo motor-driven linear robots
- servo-driven 3-axis robot
- Servo-Driven Robot
- Setup of injection machine
- Silicone Injection Molding Machine
- six-axis industrial robot
- Stainless Hopper Dryer
- Stainless Hopper Dryers
- star club
- swing arm robot
- take-out robots
- the choice between servo-driven robots and hydraulic robots will have a certain impact on efficiency
- the most popular injection molding machine
- the type of injection molding robot
- toggle clamp injection molding machine
- Toggle Hydraulic Injection Molding Machines
- toggle injection molding machine
- Top 10 brands of injection robots
- Topstar
- Topstar Engineering
- Topstar Industrial Robots
- Topstar injection molding intelligent
- Topstar Scara Robots
- Useful Injection molding machine
- Vertical machining centers
- volumetric type blender
- water chiller
- water chillers
- water distributor
- water type mold temperature controller
- Water Type MoldTemperature Controller
- Water-Type Mould Temperature Controllers
- We often face choices when performing injection molding. We will choose the type of injection molding machine
- wholesale of injection molding machines
- x carve CNC